
Thanks to the wonderful folks at MakerEd, I got to be involved with the Intel Experience Popup Store this holiday season. I was one of three “Tech Disruptors” at the Venice store (think Makers-in-Residence), who took apart old electronics and built new inventions from the parts. We came up with some fun gadgets on our own and in collaboration with people who came into the store, especially kids. There’s a special joy when children who have never seen the inside of a computer or car stereo crack into one for the first time, and it’s great to witness shy kids come out of their shells. It’s so hammered into us that you Do Not mess with technology, you Do Not void the warranty, that breaking the taboo is wildly freeing. Even the most rule-abiding is willing to join in when exclaim gleefully, “I want to see what’s inside, so I’m going to take this printer down to nothing. Want to help?” We’re curious by nature, it’s how we learn, so why on earth should we keep kids from it?
One great thing from this experience was getting to know my fellow Tech Disruptors Carlyn Maw and Jen Fox. The store’s run has ended, but we’re just getting started working together. (Last Friday I introduced Jen to the fun that is shrink plastic, and she did little else the rest of the night.)
In any case, here are some of the things we came up with:

– Circuit Board Christmas Tree. Made from some of the many circuit boards we had on hand. The dremel and I became very close during this process, we’re now BFFs. It’s created from six half tree shapes, strung together with some old wires. The colorful component ornaments were largely the work of guests and other employees at the Intel store, who all got very involved with our projects. As a final touch, I charlieplexed some LEDs and plugged the whole thing into an Arduino. A proximity sensor made the lights blink more quickly when you got up close. I’m pretty proud of our result.
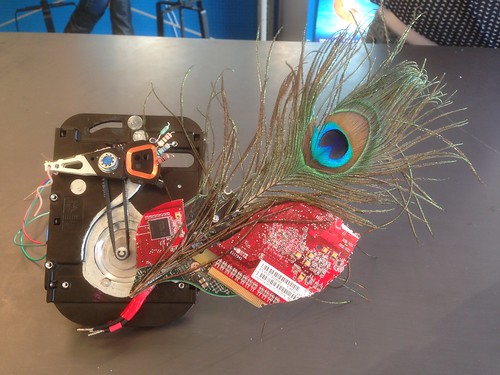
– Hard Drive Bird. It occurred to me that the actuator arm of a hard drive looks a bit like a bird’s head, so I carved up some wings/feathers from multiple colored circuit boards, and added a wire foot and peacock feather that I had lying around. I swapped out the hard drive’s motor for a different stepper motor, and rigged up a belt made from gaff tape that transfers Arduino commands from the stepper to make the bird’s head twitch. See the video!

– Gear Noisemaker. This is something that evolved over the course of my time there (and is still evolving in a current project, which I’ll get into in another post). It started out simple – a VCR motor and a cardboard gear, but quickly accumulated colorful electronic components for the gear’s face, and a plastic knife that would spin and hit whatever items we surrounded the gear with. Among the noise items: parts from a 3.5″ floppy disk, a broken cd, random metal machine bits, copper wire strings, and old wind chimes. By the end, I’d mounted the whole thing to a PVC frame, some guests added more strikers to the gear, and we incorporated it into the big Cause & Effect Machine.

– Cause & Effect Machines. Each of the Tech Disruptors was challenged to come up with and put on an event. Rube Goldberg machines are so much fun, I thought it would be an interesting challenge to try to create one. I built a seven-foot PVC pipe frame for us to build on and went nuts at dollar stores, and off we went. The first day doing this project saw the creation of a dog waterer, and when we brought the activity out for our final showcase, Jen and I made a chain reaction that used a wooden skewer marble run, a lever triggered by jenga blocks, and two big metal enclosures attached to alligator cords that closed a circuit and started my noisemaker running. Watch the videos!
Check out the full photo set on my flickr. Carlyn made very detailed posts from her time at the store, and she has a lot on her flickr stream as well.